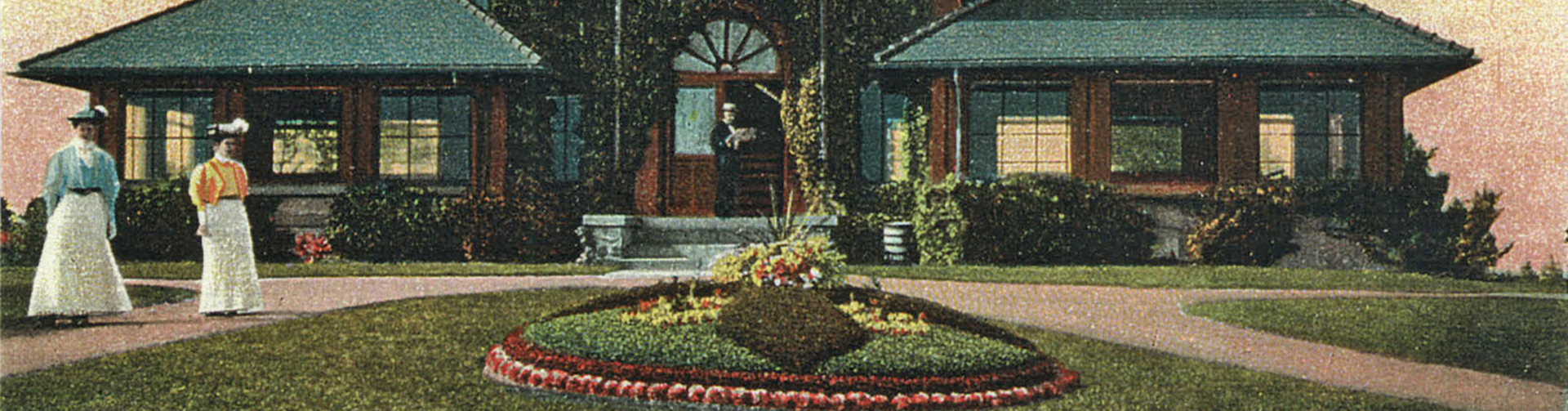
Photo Credit: from the collection of Vivian Yess Wadlin
Preserving an Icon of Prosperity:
The Story of the West Point Foundry’s 1865 Office Building
Patrick Martin, Elizabeth Norris, Rita Shaheen, Stephen Tilly, and Elizabeth Martin
During the first few months of 1865, workers at the West Point Foundry were busy casting iron cannons and shot for use in the Civil War by the United States Army and Navy. As many as 1,500 men worked in dozens of buildings packed within a narrow, forty-acre valley located within the limits of what became the Village of Cold Spring. Yet today the only building that remains of this once bustling facility is the 1865 Office Building, constructed during the wave of prosperity that marked the war years. The site’s current owner is Scenic Hudson, an environmental group that protects and enhances the Hudson River and its majestic landscape. The organization is leading an initiative to preserve and interpret the site, known as the West Point Foundry Preserve, for the public. Scenic Hudson is sponsoring historical and archaeological research to establish the factual parameters for historical interpretation, has contracted with an arborist and tree service to care for the now-forested landscape, and most recently has Preserving an Icon of Prosperity: The Story of the West Point Foundry’s 1865 Office Building acquired engineering and architectural services to stabilize the deteriorating 1865 Office Building. This article will describe the current efforts, with a focus on the Civil War-era office building.
The Foundry
After the War of 1812, the Madison administration recognized the need to expand ordnance production and stimulated the development of four foundries around the country: one in Pittsburgh; one in Richmond, Virginia; one in Georgetown, near Washington, D.C.; and one in the Hudson Valley, just upriver from the new United States Military Academy at West Point. The West Point Foundry Association, named after the most prominent geographical feature in the nearby landscape, was formed in 1817 by a group of investors led by Gouverneur Kemble. Construction and production began that year, with the first cast items available a year later. Start-up costs were supported by an advanced payment for an order of heavy artillery to be delivered to the federal government during the first few years. In addition to their ordnance products, the foundry also cast a range of other goods, including mill equipment, water systems, and a variety of domestic items. It produced numbers of steam engines, both for marine service and for use in locomotives, including the first locomotive manufactured in the United States, the Best Friend. Product lines included machinery for the sugar and cotton industries, portions of the Croton Aqueduct (to take water to New York City), the pumping engine for Philadelphia’s Fairmount Waterworks, and a pumping engine for the Brooklyn Navy Yard dry dock.1
Cold Spring is located about fifty miles north of New York City on the Hudson River. This location provided the West Point Foundry with many advantages, including easy transportation up and down the river and access to local raw materials such as iron ore, casting sand, and wood for charcoal. The young military academy across the river afforded protection during times of conflict. Finally, the foundry sat in a valley through which flowed Foundry Brook. Dropping about 100 feet vertically over a distance of 1,400 feet, from the brook provided the needed waterpower for the facility with the aid of a series of dams.
During the early years, an experienced foundryman from Ireland named William Young served as superintendent. By 1837, Robert Parker Parrott was hired to run the operation and Gouveneur Kemble reduced his direct involvement. Between 1851 and 1867, Parrott leased the West Point Foundry. As a former Army inspector of ordnance assigned to the foundry, he was familiar with the challenges of ordnance production. During his management of the operations, he experimented with ordnance design; by 1860, he had developed a rifled cannon commonly referred to as the Parrott gun—a cast-iron gun with a rifled bore and a wrought-iron reinforced breech. It spun its close-fitting projectiles as they exited the bore, resulting in greater range and accuracy than comparable smoothbore weapons of the time. The wrought-iron reinforcement of the cannon’s breech allowed Parrott guns to withstand the increased pressure generated by the tightfitting projectiles. This weapon was highly favored by the Union military.
The foundry manufactured 2,500 Parrott guns by 1865.2 Just four years earlier, a reporter for Harper’s Weekly estimated that foundry workers produced twenty-five cannons and 7,000 projectiles a week.3 During the height of the Civil War, the U.S. Army and Navy each spent as much as $100,000 during some months on West Point Foundry guns, projectiles, and gun carriages. The Parrott gun not only brought the West Point Foundry fame during the war, but also generated significant profit and capital. The primary expression of that capital was in the form of a brick office building, constructed in 1865 on the eastern bank of Foundry Brook within the foundry complex. This new office building, which replaced a smaller office located in the heart of the complex, was a deliberate expression of the foundry’s prosperity during the war.
The Office Building
The office building is labeled “office.1865” on a cast-iron sign mounted above the main entrance. Parrott decided on a brick construction and spared no expense, including a detailed plaster and wood interior that only survives in pieces today. It was an elegant, “white collar” building on a “blue collar site.” The Italianatestyle brick structure is consistent with mid-nineteenth-century commercial and civic buildings like those illustrated in Samuel Sloan’s 1851 pattern book, The Model Architect. The two-story building is composed of two wings, a symmetrical front with a central tower and a more utilitarian rear portion. The front (western) facade is finished in a higher grade of brickwork than the other three sides. The main entry, centered under the tower, is reached via stairs and a bridge over the stream. The tower housed a large cast-iron bell that used to call foundry employees to and from work. (It has since been removed to the local school.) The ground floor contains two parlors on the right and a large, grand room on the left. Existing flue penetrations indicate that these were likely heated by wood- or coal-burning stoves. The office building also contained a walk-in safe to store company and employee money. Surviving photographs from the late nineteenth century show fashionably dressed women sitting in one of the parlors, which was fitted out as a manager’s office. The finishes in the room, and the surviving fragments, are similar to those of other high-end mid-nineteenth-century residences and commercial buildings throughout the Hudson Valley. In addition to managers and their assistants, occupants were likely accountants and cashiers (near the walk-in safe) and draftsmen laying out the patterns that would be fabricated in the pattern shops.
The West Point Foundry’s 1865 Office Building is a symbol of the foundry’s peak of production and the beginning of its demise. After the war, the foundry canceled the government’s outstanding contracts, absorbing a substantial loss. Moreover, the rise of steel production in the late nineteenth century curtailed demand for cast-iron products in both the private and public sectors. Foundry operations gradually slowed during the late nineteenth century and ceased early in the twentieth century. A variety of tenants, including a silk-dying works, continued to use the building during the early twentieth century. However, by the 1940s it was abandoned.
The building fell into ruin over the next fifty years from neglect and deterioration. When Scenic Hudson purchased the eighty-seven-acre property in 1996, the structure was given immediate attention. To help arrest further deterioration, a temporary roof was installed and the distinctive bell tower was removed and covered. Scenic Hudson is committed to preserving the building, which serves as an icon for the West Point Foundry Preserve, and to transforming this former industrial landscape into a dynamic hands-on educational resource.
Research
To learn more about the history of the site, a long-term research program begun by Scenic Hudson engaged the Industrial Archaeology faculty at Michigan Technological University (MTU). Since 2001, archaeological research at the foundry has been directed toward two parallel, yet complementary objectives. MTU field school crews are excavating the site to recover technical details on foundry operations as well as to learn about everyday life among foundry workers. Drawing together diverse lines of evidence will help narrate the story of this early industrial workplace and contribute to a wide range of academic discussions in industrial and historical archaeology, the history of technology, and the cultural anthropology of industrial communities. Concurrent with these academic goals, Scenic Hudson is developing a strategy for the site’s public interpretation, which will draw visitors who want to learn about the contributions the West Point Foundry made to local, national, and international events. MTU archaeological researchers form one part of this developing interpretive plan. Field staff and volunteers speak casually with visitors about site history and the research process, discuss interpretation with members of the local community, and contribute ideas about what and how the site’s elements should be interpreted.
During the 2003 and 2004 field seasons, MTU archaeologists investigated the 1865 Office Building. Each summer, two excavation units exposed portions of the building’s foundation and helped illuminate the construction and destruction history of the building. Excavation units contained evidence of drainage pipes, architectural elements such as multicolored roofing slate and window glass, and chemical bottles from the silk-dying factory. The building has settled over time, and archaeological evidence indicates that the foundation in the back of the building was more substantial than that of the front, which has caused the front to drop. By identifying a burned layer of soil in the back of the office, MTU students also confirmed the suspicion of a fire sometime in the twentieth century.
In 2003, Scenic Hudson contracted with the firm of Stephen Tilly, Architect, to prepare a condition-assessment report and an adaptive-reuse study for the building. From May through July 2003, a team from the Tilly office and a structural engineer from Robert Silman, Associates, reviewed materials collected and prepared by MTU, as well as the holdings of the Putnam County Historical Society & Foundry School Museum. They also examined the condition of the office building and some of the outlying masonry structures at the preserve.
The archives held little documentation of the office building itself—scant drawings and a few photographs, some in which the building is a tiny detail. The team has not been able to determine the name of the architect, if there was one. The structure held forensic riches for the architects and engineer, however. Its advanced state of deterioration had the virtue of revealing to the team otherwise concealed aspects of the building’s construction. Primarily, the building’s state underlined the urgency of proceeding with a significant stabilization program.
The architectural team’s approach to the ruin mimicked MTU’s archaeological explorations of the site—a careful peeling back of material and testing of hypotheses as work proceeded. Ghosts of stair stringers and floor joists revealed the location of the rear wing’s second floor. The action of vandals and weather helped the team discover that the builders employed plaster lathing for a structural purpose and incorporated bits of cast-iron scrap in the construction. Interwoven bricks at the junction of the two wings confirmed their contemporaneity. The structure shows some major fault lines, but surviving original crack patching in the interior plaster suggests that this settlement occurred early in the building’s life and has not continued. The ten-inch tilt off vertical observed by the team at the northwest corner, therefore, is of long standing.
Preservation
There were two major threats to the building’s survival: large, vulnerable trees on an adjoining hillside that were aimed directly at the front wing and large holes in both first- and second-floor assemblies that might not provide enough resistance to prevent the two stories of weakened masonry walls from falling in. A qualified contractor removed the trees, which were among sixty-five trees in various locations around the site that had been identified by an arborist as hazards. The architectural team prepared detailed drawings to guide the stabilization. Since the stabilization scope exceeded the available budget, the documents incorporated a triage system that allowed the contractor and design team to shift their emphasis to the highest priority items that emerged as the actual work proceeded from an extensive cleanup of debris from previous collapses to selective demolition, temporary shoring and scaffolding, and finally structural rehabilitation and restoration.
The contractor’s scope included careful documentation, with drawings and photography, of conditions prior to, during, and after the stabilization process. All salvageable materials that were removed or uncovered in the debris sorting during the stabilization process (including timbers, bricks, and window casings) were stockpiled for future use when the building’s future is determined. Though the site is listed on the National Register of Historic Places, the building is not. However, all work was carried out in conformance with the Secretary of the Interior’s Standards for Rehabilitation.
Those standards define rehabilitation as “the process of returning a property to a state of utility, through repair or alteration, which makes possible an efficient contemporary use while preserving those portions and features of the property which are significant to its historic, architectural, and cultural values.” The stabilization strategies were also designed to be consistent with three possible future “contemporary uses” for the building that the team presented to Scenic Hudson:
1. Stabilized Ruin–a three-dimensional landscape. The building would be an unheated, open-air structure with only its ground floor accessible to the public. The rear wing would be a walled garden with stabilized walls and an earthen or paved floor. The building could be electrified for night lighting and exhibits, possibly including son et lumiere. Open to the elements, and without permanent occupants, the building in this case would require protection. While the site in this state would capture the romance of the ruin and evince the post-1865 battle between nature and the built environment, the stabilized ruin would also require a significant investment in interpretation to tell its story to visitors.
2. Hybrid—a restored front wing and a stabilized walled-garden courtyard in the rear. The front wing would be enclosed and fully rehabilitated for public use on the ground floor and limited office use on the upper floor. The rear wing would be treated as a stabilized ruin. Preserving the ruined portion would help engage visitors in the processes that have been acting on the building and the site as a whole, in addition to being a significantly less costly option than the reconstruction of the rear wing. The rehabilitated and occupied front portion would convey the heady days of its original construction, and it could balance and protect the more poignant and vulnerable rear-wing ruin.
3. Full Restoration. The front wing would be enclosed and restored, and the rear wing completely reconstructed. This is the most ambitious project, and in all likelihood the most expensive. A possible drawback is that a polished, complete building might dampen the imaginative connections and conjecture possible elsewhere on this intriguing site. It might sacrifice some of the compelling qualities of the ruin, evidence of the battle between man and nature that characterizes the site’s history.
All three scenarios will include the reinstallation of the restored or reconstructed bell tower cupola and development of handicapped accessibility to the 1865 Office Building. Each option offers unique opportunities and challenges, including how the building’s use relates to the larger site and to a visitor’s experience, and how the management and operations of each would be undertaken. At present, a chain-link fence to deter vandalism surrounds the building, and tours are offered periodically by Scenic Hudson. By virtue of its recent stabilization, the building has been strengthened, protected, and allowed to breathe. As archaeology on the site proceeds, and as a plan for public access is developed, the 1865 Office Building is positioned once again to play an instrumental role at this historic site. The building will draw visitors into a landscape that provides an immediate connection to our past and the West Point Foundry’s role in shaping our nation.
Footnotes
1. Factual evidence included in this short essay stem from research done by Rutsch, Edward, et al. The West Point Foundry Site Cold Spring, Putnam County, New York. Newton, New Jersey: Cultural Resource Management Services, 1979.
2. Robert Parrott, Heavy Ordnance. Reports of Committees of the United State Senate Second Session,38th Congress, Joint Committee on Conduct and Expenditures of War, 1865, Senate Report No.142, Part 2, Serial I 213, p. 137.
3. Harper’s Weekly Vol. 5, No. 246, September 14, 1861, p. 580